At its core, CNC milling includes the elimination of material from a workpiece via a series of collaborated activities. The process starts with the layout of a 3D model utilizing computer-aided layout (CAD) software. This version serves as the plan for the milling machine. When the layout is completed, the driver uses computer-aided production (CAM) software program to translate the CAD design right into a set of guidelines that the CNC machine can check out, commonly in the type of G-code. This code determines the movements of the maker's cutting devices, such as spindle turning and feed rates, making sure that every cut is replicable and precise.
One of the standout attributes of CNC milling is its convenience. Unlike standard milling makers, which normally operate along one or two axes, CNC milling devices can operate on multiple axes simultaneously-- commonly three, 4, or also five.
Check out cnc milling guide the transformative world of CNC milling, a technology that combines precision and automation to produce high-quality parts successfully from numerous materials, and find its processes, benefits, and vital factors to consider for success in modern-day production.
The choice of devices is an additional vital aspect of CNC milling. The appropriate device choice can significantly influence the high quality of the finished item and the effectiveness of the machining process.
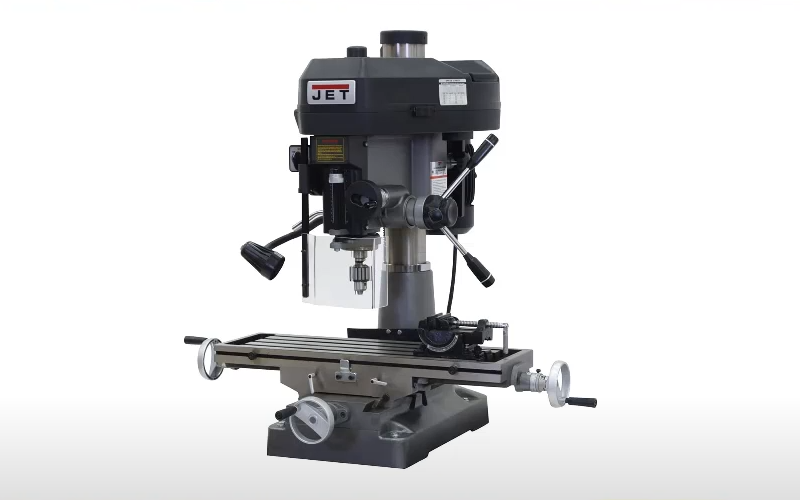
One important aspect to consider in CNC milling is worldly compatibility. Recognizing the homes of the material, including its solidity, machinability, and thermal conductivity, allows drivers to optimize the milling procedure and achieve premium results while lessening wear and tear on tools.
Beyond the technological variables like design, tooling, and products, there are additional considerations for maximizing CNC milling operations. Making use of advanced attributes such as toolpath optimization methods can streamline the milling procedure better, making it possible for quicker machining cycles and lowering waste.
Moreover, among the substantial advantages of CNC milling is the capacity to automate repetitive jobs, which decreases human error and boosts production uniformity. While conventional milling equipments require an experienced driver to look after the production procedure, CNC milling equipments can run unattended, carrying out pre-programmed guidelines with precision. This degree of automation not just improves effectiveness however additionally frees up competent employees from ordinary tasks, allowing them to focus on better tasks such as quality assurance and process enhancement.
Regardless of its advantages, transitioning to CNC milling is not without challenges. Initial economic investment can be considerable, with expenses related to getting CNC devices, software application, and skilled workers training. Nonetheless, many companies discover that the long-lasting savings related to boosted performance, reduced material waste, and enhanced product quality outweigh the initial expenses. The schedule of renting choices and budget-friendly entry-level CNC milling makers has made it much more available for mid-sized and tiny organizations to embrace this innovation.
Training and ability advancement for personnel operating CNC milling equipments are additionally vital for taking full advantage of the roi. Operators need a strong understanding of both the CNC equipment itself and the software program being utilized for programs and tracking. Numerous manufacturers find success by supplying in-house training programs or partnering with external training companies to outfit their teams with the necessary abilities and knowledge.
In recent times, technical improvements continue to shape the area of CNC milling. As sectors progressively transform to automation, incorporating functions such as synthetic intelligence (AI) and artificial intelligence into CNC machines can additionally improve the accuracy and effectiveness of milling procedures. Smart CNC systems, which include sensors and information analytics, can check performance in real-time and make instant adjustments to enhance machining parameters or to identify damage on tools. This data-driven strategy holds the prospective to significantly lower downtime and maintenance prices while improving overall performance.
Improvements in software are constantly narrowing the space in between style and production. Modern CAD/CAM systems now give a lot more instinctive interfaces and boosted simulation capabilities, enabling operators to picture machining procedures before they are implemented. By spotting potential concerns in the design stage, firms can fix layout defects or maximize cutting methods without sustaining expensive modifications to physical materials.
In the context of CNC milling, sustainability is likewise obtaining significance as makers look for methods to minimize their environmental effect. Applying methods such as maximizing cutting specifications, using much more reliable tooling, and recycling materials can add to an extra sustainable milling operation. In addition, technologies such as additive manufacturing are being checked out combined with CNC milling, presenting chances for hybrid production strategies that further improve sustainability by decreasing waste.
Explore benchtop milling machine the transformative world of CNC milling, an innovation that incorporates precision and automation to create top notch components efficiently from different products, and uncover its processes, advantages, and essential factors to consider for success in modern-day manufacturing.
In final thought, CNC milling stands for a crucial asset in contemporary production, giving companies with the ability to create complicated and high-grade components successfully. Its mix of accuracy, convenience, and automation has actually made it a staple in sectors varying from aerospace to automotive, medical to consumer products. Understanding CNC milling begins with a solid structure in its procedures, consisting of the interaction in between layout, tooling, products, and software program. As modern technology proceeds to advance, the possibility for skilled operators to leverage these advancements will just broaden, enabling better performances and advancements in CNC milling applications. By remaining educated on finest techniques and arising innovations, makers can place themselves at the leading edge of this vibrant market and completely make use of the abilities that CNC milling uses. Ultimately, successful integration of CNC milling machinery, skilled workforce training, and smart automation leads the means for the future of production, where sustainability, efficiency, and quality come to be the characteristics of functional excellence.